Century Enka: Reinforcing sustainable strategies
- Copy
Circular economy may be the latest buzzword in ESG practices, but Century Enka has been able to take it further by pioneering a process that makes nylon tyre cord fabric (NTCF) out of recycled nylon waste.
NTCF, which is used for reinforcement in vehicle tyres, conventionally uses caprolactam, a material made from crude oil, as raw material. To reduce the use of fossil fuels, Century Enka spent a year in R&D to create NTCF out of 100% recycled nylon yarn waste. This process enables conservation of fossil fuels and reuses polyamide waste, thus making the nylon yarn and tyre sectors more sustainable. The first batch of the green product was shipped in November 2022 to M/s. Apollo Tyres.
The idea was to conserve crude oil, a finite natural resource, for making virgin caprolactam and also avoid misuse of polyamide waste – which is highly detrimental to the environment. I am proud of our teams for this remarkable achievement.
Mr. Suresh Sodani, Managing Director
Century Enka’s NTCF is used by some of the biggest tyre brands in the country, including Apollo Tyres, MRF, Ceat Tyres, Goodyear, JK Tyres, Metro, and Balkrishna Tyres. Mr. Milind Ashtaputre, Senior Vice President (Marketing), shares, “We have expanded very quickly in the reinforced nylon sector and now command about 27 percent market share in India. Our success in this sector comes from our business philosophy of building meaningful partnerships with our customers.”
By creating a more environment-friendly version of NTCF, Century Enka is in a position to make the auto tyre sector more sustainable and eco-friendly. Mr. Sodani says, “We have a partnership with Apollo Tyres and they have recently created a tyre with 75 percent NTCF made from our recycled caprolactam. We have supplied MRF, one of our largest customers, with trial rolls and we are also working on similar developments at MRF and JK Tyres, and we are hopeful that we will start commercial supply to them in the near future.”
Formed in 1967 under the leadership of Mr. BK Birla in partnership with Akzo Nobel, Century Enka is now part of Aditya Birla Group. Up till 1986, the company produced only textile yarn. Now, it makes nylon filament yarn for the apparel industry and NTCF for the auto sector out of its two plants located in Pune and Bharuch.
Focus on continuous improvement
Century Enka's technological capabilities are what make it an industry trailblazer. Mr. Suresh Sodani, Managing Director, Century Enka says, “Our partnership with Akzo Nobel has provided us with a solid technology base on which we continue to improve. Our plants have the state-of-the-art technology necessary for maintaining consistent and constant quality.”
Our partnership with Akzo Nobel has provided us with a solid technology base on which we continue to improve. Our plants have the state-of-the-art technology necessary for maintaining consistent and constant quality.
Mr. Suresh Sodani, Managing Director
Mr. SY Agasimani, Plant Head, Century Enka, Pune explains, “We have upgraded to the latest technology to improve the process and maintain quality. We have shifted from a two-step manufacturing process to a one-step process, which has brought down the cost of production while improving the quality of the output.”
Environment-first approach
Many of Century Enka’s biggest successes can be found in its journey towards greater sustainability, such as the NTCF initiative and several other environment-friendly measures. Mr. Sodani asserts, “We stand by our commitment to society and we are continuously working towards reducing the environmental impact of our processes.”
We stand by our commitment to society and we are continuously working towards reducing the environmental impact of our processes.
Mr. Suresh Sodani, Managing Director
Sustainable manufacturing practices:
Century Enka has been consistently recognised for its initiatives in water reduction, energy consumption and usage of renewable energy.
- Zero liquid discharge – An effluent treatment plant enables Century Enka’s manufacturing process to achieve zero liquid discharge. All the water required during the process is used, reused, and recycled back to the cooling towers and other applications. In the last three years, it has cut consumption of freshwater by over a third.
- Biodegradable fuel – Century Enka is one of the few companies in India that uses biodegradable briquettes to generate steam for the plant. The technology for this process has been developed in association with Thermax. These biodegradable briquettes are environmentally friendly, sustainable, and have a smaller environmental impact.
- Hazardous waste treatment – The plant used to send out almost 950 tonnes of hazardous waste for disposal every year. Around three years ago, a dryer was installed to dry out the sludge before disposal. This step reduces the weight of hazardous waste by 80 percent. Earlier, waste from the nylon recycling process was sent to the incinerator for disposal. Currently, this waste is being sent to a co-processor to be converted into a high-calorific fuel for cement companies.
- Energy conservation – Along with initiatives for boosting power-efficiency, the company is looking at sourcing renewable power, a mix of wind and solar power, to reduce the plant’s dependency on grid power.
The reimagining of NTCF came out of the fact that the company is one of the largest consumers of caprolactam in the country. Century Enka recognised the need to find ways to reprocess nylon scrap as a replacement for virgin caprolactam. Mr. Ashtaputre says, “Using the technology from Akzo Nobel, our technical team has worked extensively to bring the quality of the reprocessed caprolactam close to virgin caprolactam. And we have been successful in the commercial sale of recycled caprolactam and the yarn produced from it.”
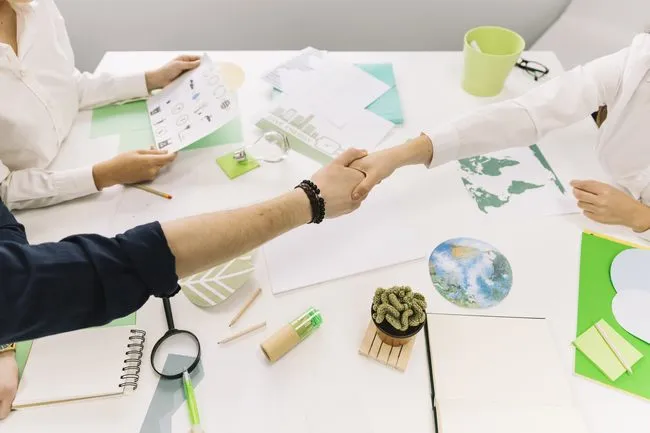
Green benefits
An incredible achievement, this recycling process has a two-pronged benefit – it conserves crude oil from which caprolactam is derived and reduces hazardous polyamide waste generated during the process.
Century Enka’s pioneering move has benefits beyond auto tyres. Textile yarn manufactured from reprocessed caprolactam has also generated commercial interest, especially among apparel brands that value its sustainability and earth-friendly attributes.
Future perfect
The company's sustainability journey is keeping it future-ready. FY22 was a record year in terms of production, sales and profitability, which has prompted a capex expansion at the two plants. Mr. Sodani shares the company’s strategy, “We want to launch polyester tyre cord fabric, which is used to reinforce passenger vehicle tyres. We will commission that plant at the end of 2023 and increase our capacity over a period of time. We hope that that these expansions will enable our future growth and entry into new segments.”
Now part of Aditya Birla Group, the company is looking forward to match synergies with different Group companies. A blend of legacy and modern, Century Enka is on the cusp of big things.