Circular economy in action
- Copy
As the world continues to grapple with the challenges posed by climate change, sustainability has become a crucial focus area for businesses across the globe. Aditya Birla Group is proud to be at the forefront of this movement. World Recycling Day (18 March) is an opportune moment to highlight some of the significant recycling initiatives undertaken by Aditya Birla Group businesses. These initiatives aim to reduce waste, conserve natural resources, and promote circularity.
Mettle to recycle
Hindalco, the metals flagship of the Group, and its subsidiary Novelis, together lead the way in aluminium and copper recycling. Aluminium can be infinitely recycled without any loss in quality, and Hindalco’s downstream units in India and Novelis’ units abroad have dedicated aluminium recycling and remelting facilities.
The Birla Copper facility at Dahej also undertakes recycling of copper scrap and recovery of copper from the slag generated from its manufacturing operations. Hindalco is also working towards increasing the percentage input of recycled material in its production via reverse supply contracts with select customers who send back their aluminium scrap for recycling.
Novelis currently leads the world in aluminium recycling with 57% of its production coming from recycled aluminium. Over the past decade, it has invested approximately $2 billion to grow its total recycling capacity to 2.5 MT.
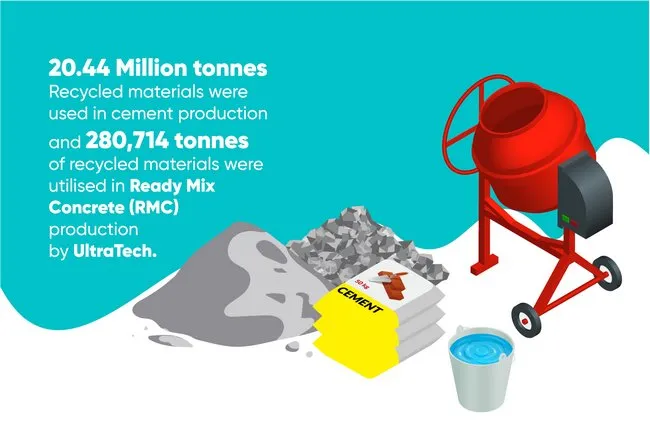
Turning waste into value
Bauxite residue, also known as red mud, is a by-product generated from the alumina refining process. To make red mud usable in the construction sector, filtration technology is employed to reduce its moisture content. Hindalco has partnered with multiple cement companies, including the Group’s subsidiary UltraTech Cement, for the use of its red mud in their cement manufacturing processes. Consequently, in FY 2021-22, Hindalco was able to utilise 62% of its red mud.
UltraTech also utilises other industrial and municipal wastes as Alternative Fuel and Raw material (AFR). It has replaced naturally occurring limestone with waste materials like fly ash, conditioned wet ash, slag and gypsum.
Additionally, the waste materials that would have otherwise gone to landfills are being used as thermal substitution in kilns, which is the most energy-consuming stage of cement production. 3.74 lakh MT of hazardous and non-hazardous wastes from other industries and 74,187 MT of Municipal Solid Waste (MSW) have been utilised in kilns in FY21, thereby reducing the use of fossil fuels. UltraTech also co-processes its plastic waste in kilns, making the company 2.2 times more plastic positive.
Bringing circular economy to fashion
Birla Cellulose, a part of the Group’s flagship subsidiary Grasim, has made significant strides in sustainability through Liva Reviva, a product that is certified by the Recycle Claim Standard. Birla Cellulose achieved a breakthrough in the manufacturing of Liva Reviva by using cotton fabric waste and following the principles of circularity. Through in-house trials with textile waste at its R&D centre, the company discovered blends of textile waste and wood pulp, resulting in recycled fibre that contains 30% textile waste — which would have otherwise gone into landfills.
Solution to the global thermoset waste problem
In materials science, a thermosetting polymer, or a thermoset, is a polymer that is obtained by irreversibly hardening a soft solid or viscous liquid prepolymer (resin) through a curing process. Simply said, it is a polymer that irreversibly becomes rigid when heated. Thermoset waste, unlike thermoplastics, is not recyclable.
Globally, 5 million tonnes of thermoset waste are generated every year, which either end up in landfills or are processed by energy-intensive methods that add to the pollution. Recyclamine® is an innovative technology developed by Aditya Birla Chemicals (Advanced Materials) to address this issue. Recyclamine® is a novel amine-based curing agent that contains specifically engineered cleavage points at cross-linking sites, which converts thermosetting epoxies into thermoplastics under specific conditions, thus helping achieve recyclability of thermosetting composites. Valuable components in a thermoset composite such as carbon fibre, glass fibre, and plastic material can be recovered and reused. This not only diverts them from landfills or incineration, but also contributes towards a circular economy.
Aditya Birla Group takes great pride in leading the way in innovative, cutting-edge recycling initiatives. The circular economy practices adopted by all its companies are a testament to the Group’s unwavering commitment to sustainability and responsible business practices.
*All data and facts mentioned are from public disclosures recorded in Aditya Birla Group ESG performance report 2021