Moving towards water positivity
- Copy
The banks of the river Chambal are home to Grasim’s first viscose staple fibre (VSF) manufacturing plant set up in 1954 at Nagda, Madhya Pradesh. Nagda had always been a water-stressed region and the company started noting how water scarcity was becoming more evident.
Over the years, Birla Cellulose, the business running the Nagda plant built reservoirs and dams to harvest rain water while optimising its own water consumption. This ensured that the surrounding communities had enough water throughout the year. But Grasim’s water story didn’t stop there.
In a bold move, the Nagda unit committed to reducing its water intensity by 50 per cent by 2025. And that vision has already paid off. Today, the unit uses less than 20 cubic metres of water to produce a tonne of fibre, an amount far lower than the EU-BAT standard of 35-70 cubic metres of water per tonne of fibre.
There are similar stories of drastic water reduction at Hindalco Industries, Aditya Birla Fashion and Retail Ltd. (ABFRL) and UltraTech Cement Ltd.
This World Water Day, we take a look at how these Aditya Birla Group companies have set global benchmarks in water conservation and are now headed towards a water positive future.
Birla Cellulose's 4R principle
VSF manufacturing is a water intensive process. It requires continuous access to a large quantity of water. Birla Cellulose adopted a 4R principle (reduce, reuse, recycle and regenerate) in its operations for closing the loop on water. The company designed several breakthrough low-water technologies that reduced water consumption significantly and helped in recovering the used water. The recovered water had better quality than the raw water from the river.
The 4R Principle
- Reduce – Low-water technologies for fibre washing, chemicals recovery and cooling tower
- Reuse – Circular technologies to reuse water several times in finishing and recovery processes
- Recycle – Membrane-based technologies to recover water
- Regenerate – Water harvesting to regenerate ground water
- Regenerate – Water harvesting to regenerate ground water

The impact
- 34% reduction in water consumption from FY 2015 to FY 2020
- 60% reduction in water intensity of its operations in the last 5 years
Grasim’s Zero Liquid Discharge processes
Birla Cellulose is currently working on creating the VSF industry’s first zero liquid discharge system at Nagda. The energy efficient system will treat waste water for reuse, while also recovering salts that can be used in several applications.
The Group has several ZLD plants to its credit. The ZLD revolution was pioneered by Grasim’s Chlor-Alkali division in Renukoot, Uttar Pradesh. Water scarcity, increasing water tariff, impact on source water, government regulations and the need to make the business sustainable pushed the unit to adopt ZLD.
Grasim's 1st ZLD plant- Chlor-alkali division, Renukoot
- Pioneered ZLD at the Aditya Birla Group
- Reduced effluent generation by 85%
- Reduced fresh water consumption by 25%
- Platinum Award for Eco-Innovation in Environment from Green India Awards, 2019
The ZLD system was a massive success. Effluent generation was reduced by 85 per cent and this water was reused, thus cutting freshwater consumption by 25 per cent, and saving 2,400 cubic metres of freshwater daily. Backed by the unit’s successful ZLD implementation, six other Group units are now looking to replicate these efforts.
Hindalco cuts freshwater consumption
Hindalco’s world-class alumina refinery in Belagavi, Karnataka draws water from the Hikdal water reservoir, a seasonal resource which relies on rain in the catchment areas. The unit also depends on the water supplied by the city corporation but in its absence, there is no back-up water supply. With water becoming a stressed resource, the unit decided to innovate to optimise its water usage.
Recycling was the first step and the unit built a 6,000 cubic metres lined pond to store water for treatment and reuse along with pumping facility and pipelines for the transfer of treated water from the treated water pond to the Refinery. The unit has even installed 25 waterless urinals at the facility. An on-site Sewage Treatment Plant (STP) of 450 KLD capacity has been commissioned for domestic wastewater treatment. The treated water is used for gardening in the surrounding area and staff colonies.
Hindalco's Alumina Refinery, Belagavi
- 6,000m3 lined holding pond for treated water
- 25 waterless urinals at the refinery
- 450KLD STP for domestic water treatment
The impact
- 40% reduction in freshwater consumption for operations
- Annual cost saving of Rs.24 million
- Domestic water consumption reduced by 112,500 litres/month
All these measures have helped. The refinery’s monthly consumption of 110 ML of freshwater has reduced by around 40 per cent, along with additional savings of Rs.24 million per annum for the unit.
Water neutral operations at ABFRL
In 2018, a NITI Aayog report predicted ‘Day Zero’ (a day when a place is likely to have no drinking water of its own) for 21 Indian cities by 2020. Among these, Chennai, Bengaluru, Hyderabad and Delhi were the most susceptible and the report triggered a series of operational changes at ABFRL. At that time, ABFRL set the ambitious target of becoming ‘Water Neutral’ across units by 2020.
The company installed systems for rain water harvesting and Artificial Aquifer Recharge (AAR). AAR refers to transfer of surface water to underground aquifers, which mimics the natural pattern of groundwater recharge of the water table. ABFRL uses harvested rainwater for manufacturing and domestic consumption and the remaining water is used to recharge the groundwater through AAR with the help of injection tube well and bore well recharging. In FY 2019-20, more than 43 million litres of rainwater were harvested and artificially recharged.
ABFRL’s water conservation efforts
- Installed rainwater harvesting and Artificial Aquifer Recharge systems across units
- Dry operations without effluent discharge
- Sewage recycling across facilities
The impact
- Became ‘Water Neutral’ by 2020
- Harvested and recharged 43 million litres of water in FY 2019-20
- Recycled 96 million litres of water in FY 2019-20
ABFRL’s manufacturing process does not generate discharge or effluents. But the company recycles the sewage generated across facilities and the treated water is then reused for landscaping and toilets. These efforts have helped the company recycle over 96 million litres of water in FY 2019-20 alone.
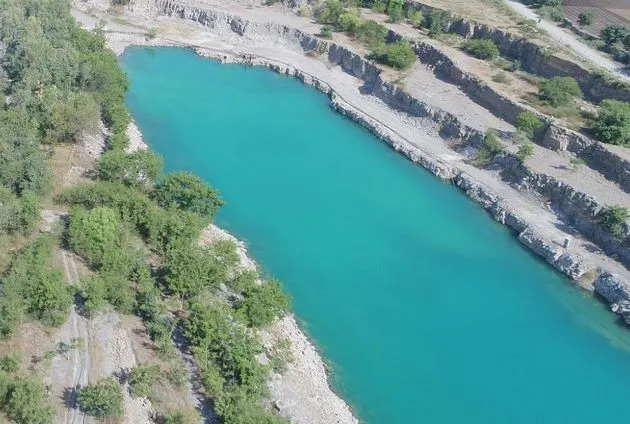
UltraTech uses mines for rainwater harvesting
When UltraTech explored the prospect of rainwater harvesting at its Vikram Cement Works in Khor, Madhya Pradesh, it ran into a problem. The underlying hard rock of the Khor and Suwakheda areas meant only 10 per cent of rainwater would seep into the ground and 90 per cent was lost.
UltraTech came up with an unusual plan in 2019-20 -- to collect the run-off water from the unit’s mining area in a pit, which would allow for rainwater to be harvested. UltraTech modified its mine planning and operations to maximise extraction of mineral from lower benches, which helped in accumulation of rainwater in these areas.
The success of this mine-based initiative – the plant harvested 8.5 million cubic metres of water in FY20 alone – has led to it being adopted by other units.
UltraTech's water conservation efforts
- Mine-based rainwater harvesting
- Watershed management in local communities
- All sites are zero-water discharge
The impact
- Over 52 million m3 of water harvested, recharged, recycled and reused in FY20.
- Recycles over 14 %of the water it uses.
- 2.8 times water positive
Water security is an integral part of UltraTech’s operations across all its sites. The company implements watershed initiatives within local communities at several sites -- Rajashree Cement Works (Karnataka), Andhra Pradesh Cement Works (Andhra Pradesh), Dhar Cement Works (Madhya Pradesh) and Baga Cement works (Himachal Pradesh).
It also adheres to a zero-water discharge policy and has invested in water recycling, recharging of groundwater and rainwater harvesting. This has led to more than 52 million m3 of water harvested, recharged, recycled and reused across all manufacturing locations in FY20.
These efforts have led to UltraTech becoming more than 2.8 times water positive. This audacious company has set its sights on becoming four times water positive by end of FY2021.
Water stewardship is integral to business operations at the Aditya Birla Group. These conscious efforts towards water conservation and preservation of freshwater reflect the companies’ resolve towards creating a sustainable future. They also embody the theme of the 2021 World Water Day – ‘Valuing water’.